Recently a Gibson Dove came in for a
great deal of work. Lots of loose braces, missing pickguard, fretwork and a bridge that had been shaved too low I guess during a previous
attempted repair.
Here we are going to show you what we
elected to do with the bridge.
The owner wasn't happy with the tunamatic that is stylistic of the period - and
asked if there was something that could be done.
The obvious choice was to replace the bridge with a modern style bridge with a
bone saddle.
|
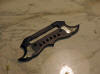
The original bridge was typical for this period
Gibson with the huge cutout for the adjustable tunamatic saddle. |
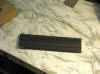
Well, this is where we start - we picked out
a bridge blank with the color and grain orientation we liked. |
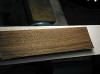
The first step of course is to trace the shape
of the original bridge onto the Rosewood blank, |
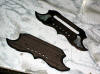
Skipping ahead a few steps - here
we can see the new bridge roughly shaped with the pin holes located and
drilled undersized. |
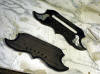
In an effort to save the customer some money
- we mutually decided that we would transfer the inlays from the old bridge
to the new one. |
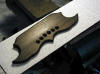
Here is a shot of the final shape of the
bridge -
The pin holes have been countersunk and the
edges have been rounded. Still needs some sanding though. |
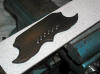
After a bit of sanding and some lemon oil -
things are beginning to look good. |
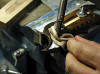
Now onto transferring those inlays.
We begin by heating the inlay with an iron and a wet cloth.
This is so we cam break the glue joint between
the inlay and the bridge. |
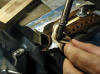
The iron will heat the inlay and the wet cloth
protects the inlay as well as providing some steam. Besides - I kind
of like the sizzling sound that it makes. |
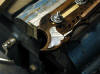
I begin poking and prodding around the inlay
with a very small dog-leg chisel.
By the way - you can see how the bridge is clamped in place to allow me to
work on the bridge without it moving around. |
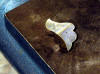
After a few minutes and enough heat/steam,
the inlay comes out in one piece with very little damage. |
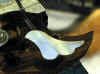
Here is a shot of the chisel getting under
the second inlay. |
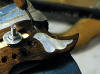
The trick here is to be patient enough to allow
the inlay to come out when it is ready. and not force it - so it doesn't
crack in half. |
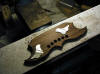
Both inlays are out and I have placed them on
the new bridge just to see how things will look. |
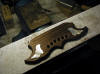
Whenever I do inlay work like this - I try to
place the inlays where I thing they will look right - then I walk away and
go do something else before I come back and see in something needs to be
adjusted. |
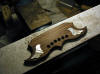
After I am confident in my choice of location
- I will need to route the inlay cavity to accept the inlays |
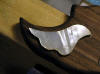
The inlay will be held in place
by a tiny drop of cyanoacrylate glue |
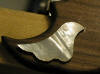
Then I can trace the inlay with a pencil.
Sometimes a scribe will be needed to trace the inlay.
In this case a pencil will do the trick since
we are not dealing with a very ornate inlay and - |
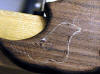
- the pencil line is visible enough to see
the outline of the inlay cavity. You can see the residue of the glue
used to hold the inlay in place. |
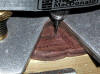
Using a Dremel tool n a precision routing
base, we begin taking material off from the inside out . |
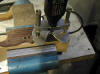
The depth of the cutting bit is set to exactly
the thickness of the inlay. After installation - I don't want to have
to make these inlays any thinner that they are. |
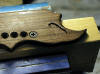
Here we can see my progress in routing the
cavity. |
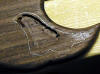
Continuing to take of material - slowly but
surely. - the anticipation is killing you - isn't it? |
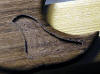
Here we have the inlay cut precisely to the
pencil line - the depth should be perfect to accept the inlay so it fits
flush with the surrounding wood. |
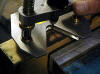
Now onto the other side - I'll spare you the
drama of the step by step routing pictures. |
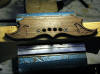
Both inlay cavities are cut. |
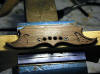
By the way - notice to two deck screw holding
down the bridge - the pin holes were countersunk early in order to accept
our screws. |
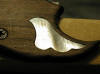
The inlay fits quite nicely without much of a
gap |
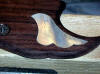
Here is a closer look. |
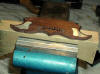
Both inlays are in and ready
to be glued in place. |
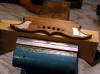
You can see that the inlays are fairly level
with the surrounding wood. |
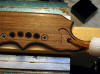
A bit of brown tinted cyanoacrylate
glue will hold things nicely. |
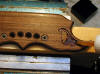
Usually inlays would be glued in
with a black tinted glue to fill the
gaps around and inlay |
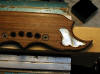
Since I had very little gap surrounding the
inlay, I figure that brown glue will blend better with the natural color
of the wood. |
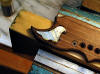
You can see the glue ooze up around the
inlay. |
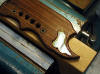
This will create it's own seal; so the edges of
the inlay are smooth |
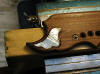
After the glue is dry we have to level off
the glue and do some final sanding |
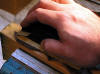
Here I am starting with some 180 grit paper
with a sanding block to do the majority of material removal |
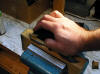
Quickly switching to 220 Grit |
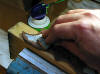
Then I'll switch to some finer grits backed
by some cork |
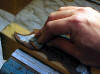
More sanding with even finer grits .. |
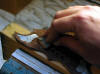
..you guessed it - even more sanding |
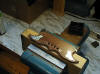
Finally we are done sanding and have the
results we want. |
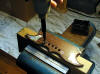
Time to remove the screws and see what we've
got. |
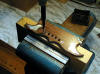
After we clean this bridge up - the only
thing left is to glue it onto the guitar - locate and cut the saddle slot
and make a saddle. |
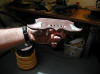
Here is the sanded bridge - still looks a bit
rough - huh? |
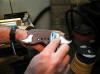
First we clean things up a bit with some
Naphtha - things are starting to improve. |
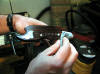
Then we start rubbing in some lemon oil to
see the final product. |
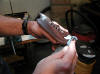
And some more oil ... |
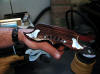
Once the bridge is saturated this is what
we've got |
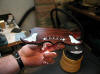
I'll give it some time to soak up the oil and
probably rub on some more later. |
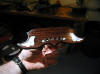
Once I think I have enough oil on the bridge
and it looks like I want it I'll set it aside to really dry well. |
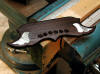
Here is what it looks like when it is finally
dry. A thing a beauty. |
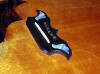
Fast forward here - I was a bit pressed for
time to complete this job so I neglected to show you the steps where we cut
the saddle slot. |
Not to worry - I have several more bridges in
house to make - I'll show you how we cut the saddle slot in a future
article. |
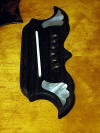 |
Here is the bridge glued onto the guitar with
a compensated saddle - ready for strings. |
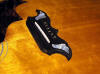
A pretty good match to the original - in size
shape and color. The only thing missing is that horrible tunamatic and
all the related hardware. |
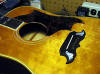
This should improve the tone of this guitar
quite a bit. |
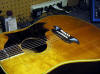
After all, the strings are now vibrating on a
bone saddle that is in direct contact with the bridge - It's all about the
transfer of energy. |
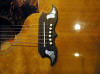
Here is a shot from overhead |
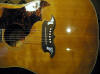
The plain white bridge pins complete the
tuxedo look - and is appropriate for what originally came on the guitar. |
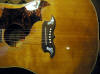
We also replaced the pickguard, the original
had disintegrated as many cellulose guards tend to do. |
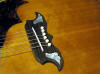
A Gibson dove originally came with a very
ornate pickguard with lots of engraving and inlays |
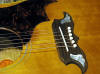
Our customer was very budget conscious
concerning the repair, so we elected to go with a plain guard made from
Tor-Tise. |
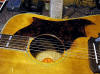
At any time in the future he can decide to
complete the work on the pickguard. For now it looks period correct -
just a bit plain. |