For some reason it
seams that Martin guitars are the most common candidate for neck resets in our
shop. Nevertheless, our candidate for this demonstration is a 1960's Martin D-18.
Need I reiterate here that this article is for information purposes only and not
a tutorial on how to do your own neck reset?
|
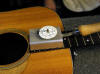
We always
start by heating the fingerboard extension with a specially made iron that
fits over the frets and heats the fingerboard. |
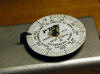
We get
things pretty hot. we usually heat things up to about 400 degrees.
Our thought here are that we want to transfer as much heat as possible in
as little amount of time. |
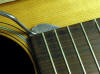
After only a
couple of minutes the glue joint softens and we are able to start prying
up the fingerboard with a small palette knife. |
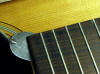
Working our
way around the corner of the fingerboard extension, the fingerboard begins
to give. |
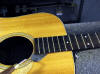
Once the end
is free we start working our way towards the neck. |
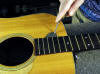
Pretty soon
we'll switch to a longer palette knife. |
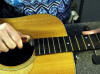
Here you can see Sharon working
the longer palette knife all the way up to the 15th fret. |
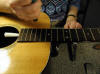
Sharon does
most all of the loosening of fingerboards in the shop - as well as
bridges, braces or anything else attached to a guitar. |
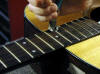
Next, we
remove the 15th fret with specially ground fret pullers. |
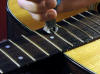
Removing the
15th fret allows us access to the dovetail joint hidden by the
fingerboard. |
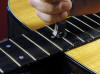
Sharon just
"walks" the fret out from one side to the other. |
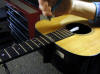
With the
fret out of the way we'll be able to access the dovetail joint without any
further disassembly of the guitar. |

Here you can see that little
Teflon wedge inserted into the fingerboard. We use it to lift the
board slightly so the softened glue doesn't re-tack while it's still warm. |
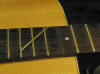
Now we are
ready to access the dovetail joint. |
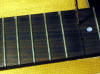
we begin by
drilling a hole straight through the fret slot into the gap between the
mortise and tenon of the dovetail. |
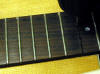
I always
drill two holes, one for the steam to go in and one for the steam to
escape |
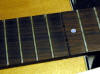
Some
luthiers like one.
I like two. |
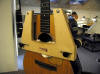
Here is a picture of the guitar
wearing the Stew Mac neck removal jig. A very neat tool that makes
the job go a whole lot easier. |
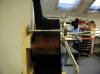
Prior to the
folks at Stew Mac coming up with this we used a home made version that was
a bit more crude, without all the fun moving and replaceable parts. |
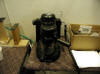
Here we have the ubiquitous Mr.
Coffee cappuccino maker. Our chosen tool for the production of
steam. |
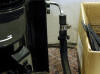
with a hose
attached to the frothing mechanism ... |
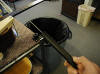
and a needle
attached to the other end of the hose ... |
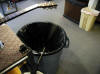
e can inject
steam directly into the neck joint. |
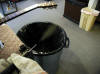
I think you
can make out the steam coming out of the needle in this picture. - I
never tried to photograph steam before.
Do I need to get out more? |
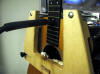
We begin
injecting steam into the dovetail ... |
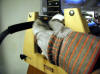
Wiping up
any drips and splatters along the way - you definitely need a good pair of
gloved for this job. |
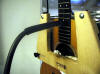
The reason
why I like two holes as I mentioned above is so the steam has a place to
evacuate rather than spit out all the other seams around the neck.
This cuts down on any finish damage that can occur. |
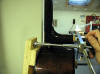
As the steam
softens the glue joint, the jig handle is turned to apply pressure to the
dovetail. |
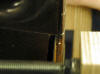
If you look
close, you can see a very small gap appearing between the fingerboard and
the body. |
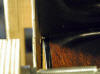
We continue
to apply steam in intervals and then apply a bit more pressure. The
gap will begin to get larger as the neck is pushed out of the heel block. |
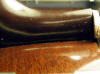
Here is a
look at the neck sliding out of the body. |
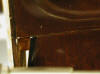
The neck has
worked it's way free of the body ... |
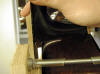
with a bit
of manual coaxing ... |
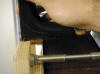
we gently
persuade the neck to let go completely. |
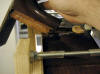
There - it's
finally out. |
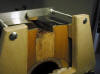
Here is a
shot of the neck-less body still in the jig. |
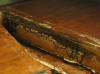
Looking
closely we can see the remnants of glue and old shims
It seems this neck has been reset once before.
|
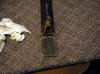
Time to
clean up the mess while the old glue is still soft and rubbery. |
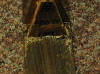
Here is a
close-up of the underside of the dovetail and fingerboard. |
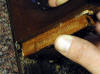
All the old
glue and yuck has to be removed from all the surfaces |
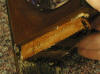
Holding a
neck while chiseling away all the old glue can be tricky ...
|
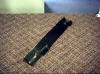
to solve the
problem we cam up with this little universal neck holder. It's
covered in leather to protect the finish. |
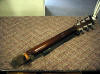
I can hold a
neck in just about any position ... |
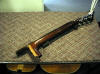
...to work
on practically any part of the dovetail joint. |
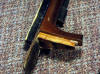
The neck can
sit firmly in any tilted position. |
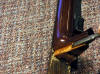
Here we
begin cleaning up the old glue. |

Chiseling
away and being very careful to remove just the glue ... |
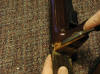
... and not
any wood. |
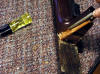
I can get
get way up into the cheeks of the heel with a smaller chisel. |
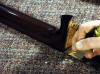
Now down to
the fingerboard, |
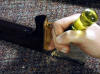
Here I am
using the chisel more like a scraper. |
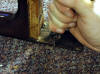
We keep our
chisels pretty sharp but as you can see we are pretty hard on then so we
don't spend much on top shelf chisels. |
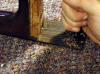
The bottom
of the fingerboard is cleaning up quite nicely. |

There we go
- clean as a whistle |
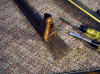
Now that the
neck joint is all cleaned up, let's move onto the body. |
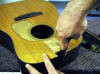
This is a
bit tricky as there is not a lot of room to move around in there. |
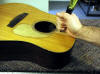
The surface
of the face that the fingerboard extension is glued to has to be cleaned
as well. |

As you can
see we spend a fair amount of time taking apart guitars. |
All of the
necks and bodies are labeled with the work order number and the customers
name. We want to make sure that the right neck goes back on the
right body. |
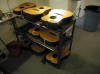
Here is a
stack of Martins all in the process of having their necks reset. |
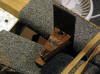
The next
step is to relieve the dovetail. This is a step that not a lot of
shops do. I like the procedure because it assures a tight fitting
look between the heel and the body when we assemble the guitar. |

The neck is
held in a jig we normally use to hold guitars upside-down. |
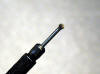
We us a
small ball end cutter to make the cut. |
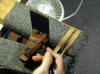
We carefully
cut a channel on the "cheeks" of the heel. |
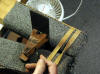
By relieving
this area just a bit, the removal of material to re-angle the neck goes
quite a bit smoother and conforms to the sides of the guitar much better.
|
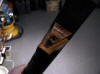
Here is a
look at the relieved part of the heel. |
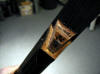
After we
re-cut the angle of the neck, the relieved area will be much smaller then
it is now. |
|
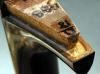
As it is we
remove very little material. |
|
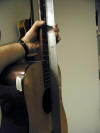
Now it's
time to start re-angling the neck. We double check the neck angle
before we start. |
|
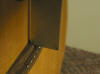
You can see
how far below the bridge the neck angle points to before we get started. |
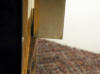
With a neck
angle this "under-set" there is no way to get a nice low action on
the guitar |
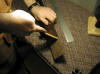
We begin by
tapering the cheeks of the heel, taking more material off the back end of
the heel and pretty much nothing from the fingerboard end. |
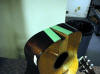
Once I have
removed enough material to satisfy me that there is improvement. we tape
off the area of the guitar that the heel comes into contact with. |
|
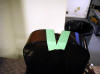
The tape
will protect the finish from the next step in our process. |
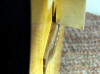
Once again
and all the way through the process, we keep checking our progress in
terms of neck angle. Here you can see that we have already improved
things dramatically by about 50 percent. |
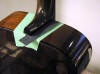
We cut
strips of 180 grit sandpaper and place it under the heel of the guitar
face up, where the heel contacts the body. |
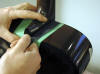
Holding the
neck firmly in the correct position, we pull the sandpaper out in one
motion. |
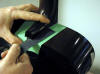
As the
sandpaper is pulled out from under the heel, it will continue to cut the
heel end of the joint more aggressively than the fingerboard end |
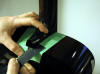
This ensures
that we will continue to improve our neck angle and also make sure that
the cheeks of the heel conform nicely to the sides of the guitar. |

Once again,
we check out progress. I think it goes without saying here that these
steps take a lot longer than is represented here. If we showed you
all the pictures of how many times we check the angle, and then remove
some more material, and then check again, and remove some more ... it
would get a bit boring woudn't it. |
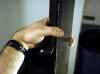
Laying the
straight edge on the fingerboard, we will be able to see where the neck
points to at the bridge. |
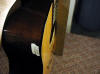
Finally
things are looking
pretty good. |
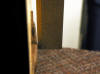
A closer
look shows us that the straight edge is pointing well above the bridge -
Perfect. |
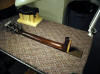
It's time to
move onto prepping the neck for re-installation. This is another step that
I find a lot of shops skip. |
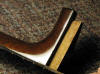
During the
course of neck removal, trimming the heel and setting the angle, the heel
can show some evidence of handling. |
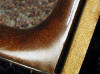
If you look
close you'll see some small chips of missing finish. This one isn't
too bad at all. In fact most shops would ignore it. |
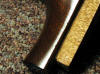
I have
always been of the belief that in this business we should (wherever
possible) try to cover our tracks and remove all evidence that a guitar
has been worked on. |
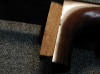
Unfortunately it's a belief that not too many repairmen share, all
together too evident in all the "teeth marks" and tool marks we see on
guitars coming into our shop having had repairs done elsewhere |
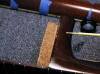
Alight -
I'll get off my soapbox.
Back to this
job. In these couple of pictures I am brushing on some lacquer to
the edge of the heel. |
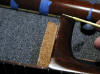
It can take
several applications and plenty drying time in between. |
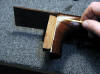
And not for
the other side. |
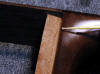
After
several applications and enough drying time, we have successfully built up
the finish taller than the surrounding area. |
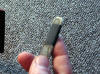
Time to do a
bit of sanding. I merely wrap a small piece of 320 grit wet or dry
paper around a polishing stick. |
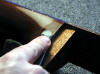
It gives me
the right kind of backing for the sanding job, |
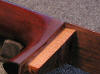
After
working up through a few grits, 320, 400, 600 and 1000 - this is what we
get. |
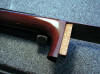
Now it's
time to compound and buff up the finish. |
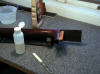
Using some
liquid compounds
I gently buff up the area. |
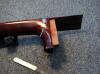
Things get a
bit sloppy while compounding. |
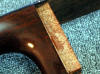
The results
are a nice shiny finish with no trace that we've been anywhere near the
neck. |

Even upon
close inspection you'll notice all those little finish chips are gone. |
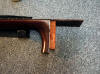
Not it's
time to re-work the dovetail and get this guitar back together again. |
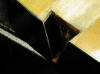
Shims are
glued in the neck. We make ours out of Mahogany. The same wood
as the heel block and neck. |
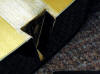
On top of
the shims, we place very thin pieces of articulating paper - the same that
your dentist uses. |

They are
glued in with a very light tack adhesive so they will be easy to remove
later. |
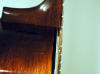
As the neck
get inserted into the dovetail, the shims are making the neck sit proud of
the body. |
The idea
here is to re-cut the dovetail tenon to exactly match the angle of the
mortise.
Not a simple
task since you can't really see in there. |
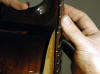
Applying
firm pressure, the articulating paper will leave it's mark on the tenon. |
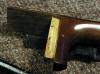
here we can
see very few spots that the tenon has contacted with the mortise.
|
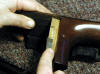
We chisel
down just the areas we know to be touching. |
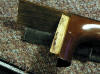
After
another fitting we can see more area has contacted the mortise. |
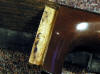
As we remove
only the "blued" area the tenon will sit a bit farther back into the
dovetail making futher contact and pulling the neck into the mortise. |
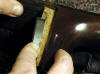
This is
perhaps the trickiest part of neck resetting. It taks a firm
understanding of the geometry involved. |
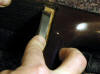
Here we are
removing a bit more material. |
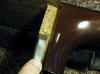
and a bit
more. |
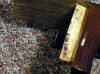
After
another fitting we see some more blue spots. |
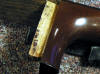
The blue
spots will shift as the tenon changes shape to fit the mortise. |
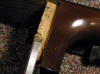
We continue
... OK - I think you get the idea hear - unless you want to see 70 or 80
more pictures like the last 10. |
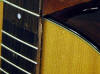
As we keep
this process up, the gap between the body and neck continues to shrink as
the tenon takes the shape of the mortise. |
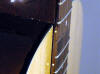
Finally we
get to the point where there is almost no gap at all. The remainder
of this tiny gap will disappear as we press the neck into the dovetail,
ensuring a very tight fit. |
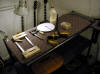
Here we are
lining up all of you clamps and gluing supplies so they are at the ready. |
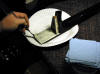
We apply a
thin coat of glue only onto the surfaces that are going to be in a bare
wood to wood contact. |
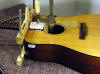
First we
clamp the fingerboard extension and check the centerline fit of the neck.
Then we get a couple of cam clamps to press in the dovetail area. |
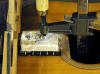
It's not
very clear in this picture because of the plastic covering on the
caul, but it is notched to fit over the frets and has a radius to match
the fingerboard. The saran wrap is so we don't inadvertently
glue it to the fingerboard while cleaning up any squeeze out. |
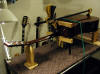
Here is our
complete clamping setup, the long clamp from the heel to the tail block is
probably unnecessary, but this setup covers all the bases, and I've always
been a big believer in insurance. |
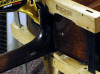
The most
important part of our clamping setup is the two cam clamps. They are
doing all the real work.
Now we wait
for things to dyr and move on to the frets. |
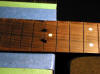
First order
of business, remember those two little holes in the fingerboard at the
15th fret? We fill them with a bit of glue and wood dust.
Looks nasty, I know. |
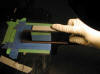
with a
little sanding in the area things will improve dramatically. |
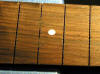
Here's what
things look like after a bit of rough sanding.
A lot
better. |
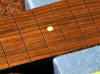
That's a big
improvement. The filled holes will be re-cut to accept the new
fretwire. |
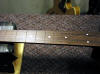
First we
plane and prep the board for frets. There are plenty of pictures
throughout this site on re-frets - step by step - so I'll spare you that
here. |
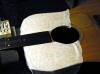
Just the
highlights for now - the face gets protected with some transfer tape.
Notice the single fret in the guitar - we were testing for the right tang
size. |
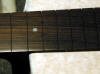
A closer
look at the 15th fret holes. Nobody will ever know we were there. |
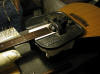
The
ubiquitous "Fret Buck"
One of the best tools I ever bought. |
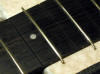
The Fretting
is going quite nicely. |
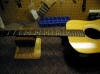
Finally all
the frets are in. |
The next
step is to do the level and crowning of the frets. There are lost of
examples of those procedures on this site
So I figured I would spare you the photos here.
|
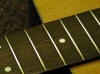
There - all
leveled and crowned. that was quick. |
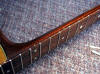
fretwork
invariably leaves a fair amount of telltale signs on the sides of the
neck. |
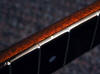
You can see
the lacquer missing from the edges of the frets. |
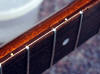
In keeping
with our philosophy that guitar repairs should always be able to be done
with as little evidence that we've "been there"
we are going to touch up the sides of the neck |
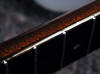
Sadly I have
seen all together too many re-frets being done out there that leave this
part of the job completely ignored. |
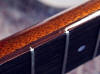
After a few
applications of lacquer, things are looking much better. |
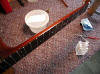
I'll be the
first one to admit that it's not always possible to do extensive repairs
without any cosmetic evidence that the work has been done. But there
is no excuse for not trying. |
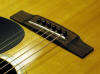
Here we are
at the end of our neck reset. A custom made bridge with a nice tall
saddle. |
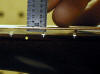
Even though
we have a fairly tall saddle - the action is now quite low.
Resulting in a very comfortable guitar to play. |
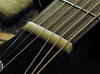
A new bone
nut tops things off quite nicely. |
|
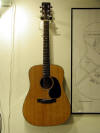
All set for
another 30 years of service. |
|
Suffice it
to say that a neck reset is a pretty complicated job. It takes a
great deal of understanding about the "geometry" of the guitar as I call
it. It also takes a tremendous amount of experience and skill to do
it well. We do about two to three hundred a year. Before
committing to a neck reset make sure you check out your luthier very
thoroughly to make sure they are up to the task. |